Understanding Wire Wound Inductors: How They Works
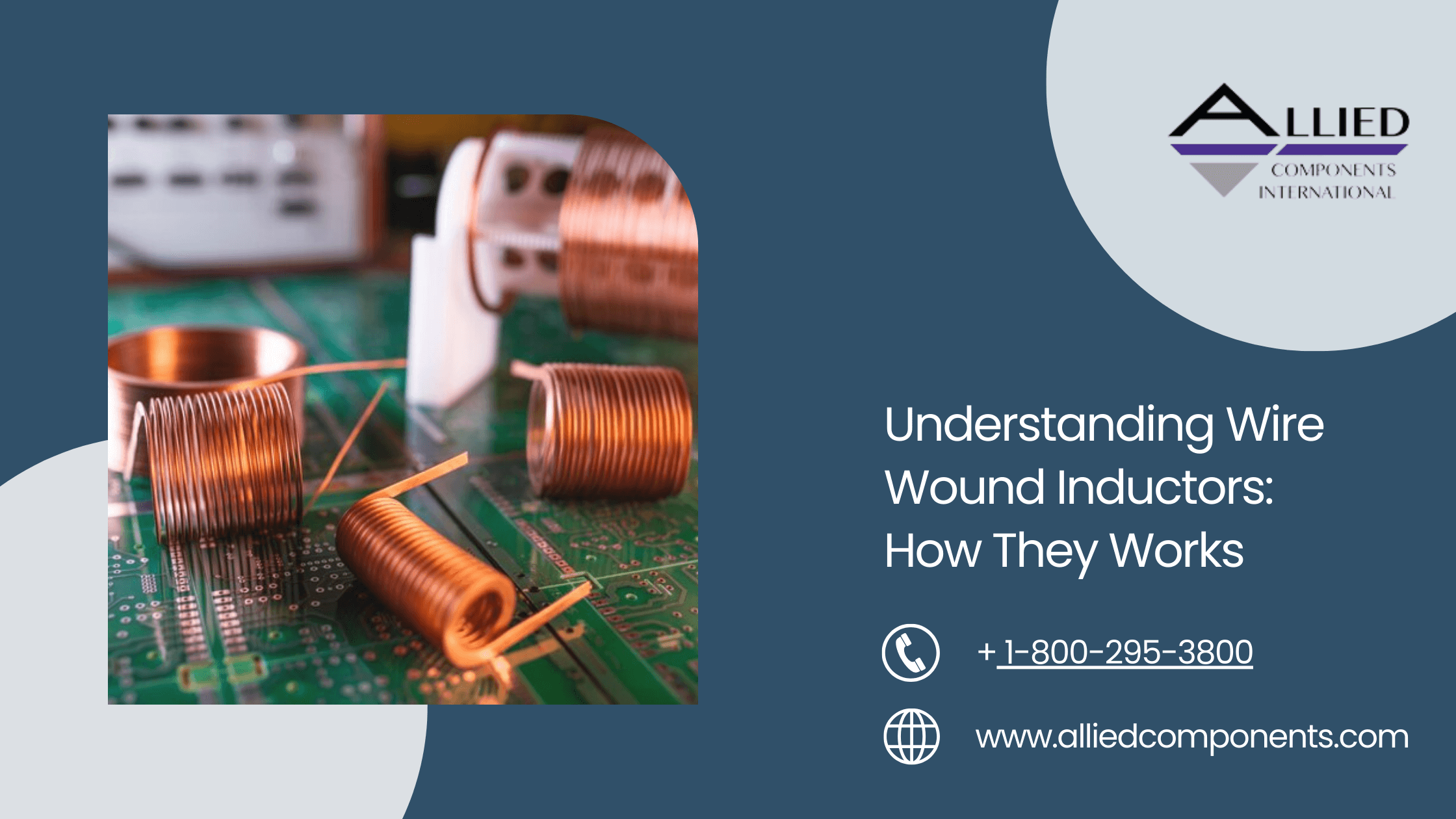
In the world of electronics, inductors play a crucial role in shaping circuits' functionality. These passive components are essential for energy storage, filtering, and signal processing. Among the various types of inductors, wire-wound inductors stand out due to their unique construction and performance characteristics.
Read on to learn about inductors, including what a wire wound inductor is, how it works, its types, applications, advantages, and disadvantages.
Understanding Inductors
An inductor is a passive electronic component that stores energy in a magnetic field when electric current flows through it, a property known as inductance, measured in Henries (H). Inductance arises from the magnetic field generated around a conductor, which induces voltage-opposing changes in current, making inductors valuable for signal smoothing and noise filtering.
Inductors are crucial in various applications, including power supplies, which filter high-frequency noise to smooth out voltage, and RF (Radio Frequency) circuits, which tune and match impedance. These are also essential in transformers for energy transfer between circuits and energy storage systems to maintain a steady power supply.
What Is a Wire Wound Inductor?
A wire wound inductor consists of a coil of wire, typically made of copper or aluminum due to its excellent conductivity, wound around a core. The core can be made from air, iron, or ferrite, each imparting different inductive properties.
The construction of wire wound inductors involves different winding techniques, including single-layer, multilayer, and toroidal winding, each offering distinct performance characteristics.
Wire wound inductors are known for higher inductance values and greater current handling capabilities than other inductor types, such as multilayer and film inductors. While multilayer inductors consist of multiple layers of conductive material separated by insulating layers and film inductors, they use thin films of conductive material. Wire wound inductors excel in applications demanding high inductance and reliability due to their superior performance and strength.
How Does a Wire Wound Inductor Work?
To understand the functionality of a wire wound inductor, it is essential to explore how it generates a magnetic field, the role of the core material, and the impact of wire turns and spacing on its inductance.
- Magnetic Field Generation
When an electric current flows through the coil of a wire wound inductor, it generates a magnetic field around the coil. The strength of this magnetic field depends on the current flowing through the coil and the number of turns of wire.
-
Role of Core Material
The core material plays a crucial role in enhancing the inductance of a wire wound inductor. Core materials like air, iron, and ferrite have varying magnetic properties.
Air cores are used for high-frequency applications, iron cores for high inductance values, and ferrite cores to balance high inductance and frequency stability.
-
Impact of Wire Turns and Spacing
The number of wire turns and the spacing between them significantly impact the inductance value. More turns and tighter spacing result in higher inductance.
The winding technique also affects the inductor's performance, with precision winding techniques offering better control over inductance values.
Types of Wire Wound Inductors
Wire wound inductors come in different types based on the core material used. Each type offers unique characteristics suited for specific applications:
-
Air Core Inductors
Air-core inductors lack a core material and utilize an air-filled space for winding. They excel in high-frequency applications requiring low inductance values and offer stability without core losses.
-
Iron Core Inductors
Iron-core inductors utilize iron cores to enhance inductance, which is ideal for applications needing higher inductance values, such as power supplies. While iron cores boost permeability, they may introduce losses at higher frequencies.
-
Ferrite Core Inductors
Ferrite-core inductors use ceramic ferrite cores, offering high inductance and stability across frequencies. Due to their balanced properties, they are versatile for RF circuits, filters, and energy storage applications.
Applications of Wire Wound Inductors
Wire wound inductors are versatile components used in various electronic devices and systems:
-
Power Supplies
In power supply circuits, wire-wound inductors help smooth out the output voltage by filtering out high-frequency noise.
-
Radio Frequency (RF) Circuits
RF circuits utilize wire wound inductors for tuning and impedance matching, ensuring efficient signal transmission and reception.
-
Filters and Chokes
Inductors are integral to the design of filters and chokes, which block or attenuate unwanted frequencies in a circuit.
-
Transformers and Energy Storage
Wire wound inductors are also used in transformers for energy transfer between circuits and energy storage applications, where they help maintain a steady power supply.
Advantages & Disadvantages of Wire Wound Inductors
Wire wound inductors offer distinct advantages and disadvantages that impact their suitability for various electronic applications.
Advantages
-
High Inductance Values: They can achieve significantly higher inductance values than other inductors, making them ideal for applications requiring substantial energy storage.
-
Stability: These inductors maintain stable inductance across frequencies and temperatures, ensuring consistent performance in diverse operating conditions.
-
Reliability: Their robust construction ensures long-term reliability, even under challenging conditions typical in power supplies and RF circuits.
Disadvantages
-
Size and Weight: They tend to be larger and heavier than alternative inductor types, which can constrain the design and portability of electronic devices and systems.
-
Parasitic Capacitance: During winding, wire wound inductors may introduce parasitic capacitance, which can degrade performance at higher frequencies, causing unwanted resonances and reduced efficiency in such applications.
Final Thoughts
Wire wound inductors are crucial components in electronics, offering high inductance, stability, and reliability. Despite the potential size and parasitic capacitance limitations, their advantages outweigh the drawbacks in many applications. Exploring and utilizing wire wound inductors in electronic designs can enhance circuit performance. Whether in power supplies, RF circuits, or filters, wire wound inductors are essential in modern electronics. Understanding their construction, principles, and applications allows engineers to integrate them into advanced electronic systems effectively.
Enhance Your Circuit Efficiency with Wire Wound Inductors at Allied Components International
Ready to elevate your electronic designs? Discover the superior performance of wire wound inductors from Allied Components International. Enhance efficiency, reliability, and innovation in your circuits today. Explore our wide range of high-quality inductors and confidently transform your electronic projects.
Contact us today for expert guidance and superior solutions tailored to your needs.